In the fast-paced world of construction, choosing the right materials can significantly impact the efficiency, durability, and overall success of a project. One material that continues to gain traction is Laminated Veneer Lumber (LVL). Known for its strength and versatility, LVL formwork is becoming increasingly popular. This article explores what LVL formwork is, its durability, benefits, maintenance, and its future in construction.
What is LVL Formwork?
Defining LVL Formwork
LVL formwork refers to a system made from laminated veneer lumber, which is engineered wood created by bonding together thin layers of wood veneers with adhesives. This process results in a material that boasts both high strength and stability, making it ideal for formwork applications in the construction industry.
The use of LVL formwork provides a robust solution for underpinning and temporary structures required during the pouring of concrete. Unlike traditional timber, LVL offers more straightness and uniformity, reducing the likelihood of problems such as warping or twisting during use. This consistency not only enhances the quality of the concrete finish but also minimizes the need for adjustments during the construction process, leading to increased efficiency and reduced labor costs.
Key Components of LVL Formwork
Several key components make up LVL formwork systems, allowing them to function effectively:
- Laminated Veneer Lumber Panels: The core material that provides structural strength.
- Steel Supports: Used to give extra strength and stability during the curing process.
- Connecting Hardware: Essential for assembling various elements of the formwork quickly and securely.
- Edge Sealing: Protects the veneers from moisture, enhancing durability.
Understanding these components helps in appreciating how LVL formwork can not only support concrete structures but also adapt to various construction shapes and specifications. Additionally, the lightweight nature of LVL panels simplifies transportation and handling on-site, making it easier for construction teams to set up and dismantle formwork systems as needed. This flexibility is particularly beneficial in projects with tight deadlines or complex designs, where efficiency and adaptability are paramount.
Moreover, LVL formwork systems are increasingly recognized for their sustainability benefits. The production of laminated veneer lumber often utilizes fast-growing tree species, which can be harvested more sustainably than traditional hardwoods. This not only helps in reducing the environmental impact of construction projects but also aligns with the growing demand for eco-friendly building practices. As the construction industry continues to evolve, the integration of LVL formwork represents a forward-thinking approach that balances performance with environmental stewardship.

The Durability of LVL Formwork
Material Composition and Strength
The strength of LVL formwork is derived from its unique material composition. Each layer of wood veneer is bonded using advanced adhesives, providing a high-performance product that excels in load-bearing applications. LVL is typically engineered to endure significant stress, making it suitable for heavy construction tasks.
This engineered wood product presents a tensile strength that surpasses traditional wooden formwork. Consequently, LVL formwork can withstand the harsh conditions of construction sites, ensuring safety and performance stability throughout the project lifecycle. The manufacturing process of LVL involves carefully selecting and orienting the wood fibers, which enhances its structural capabilities. This meticulous attention to detail not only contributes to its strength but also ensures uniformity in performance, reducing the likelihood of failures that can arise from inconsistencies found in natural wood. Read more about lifecycle on https://researchsupport.harvard.edu/research-lifecycle
Resistance to Environmental Factors
Durability is not solely about strength; environmental factors such as moisture, temperature fluctuation, and UV exposure can compromise the efficiency of construction materials. LVL formwork exhibits remarkable resistance to these factors. The adhesives used in LVL construction afford it superior moisture resistance, preventing warping or swelling that commonly affects standard timber formwork.
Moreover, LVL’s structural integrity remains intact across various temperatures, making it a reliable choice for installations in climates with extreme weather conditions. This resilience translates to fewer replacements and repairs during the formation process. In addition to moisture and temperature resistance, LVL formwork is also designed to withstand the damaging effects of UV radiation, which can degrade many other materials over time. The combination of these protective features not only prolongs the lifespan of LVL formwork but also enhances its overall cost-effectiveness, as contractors can rely on its durability for multiple projects without the need for frequent replacements.
Benefits of Using LVL Formwork in Construction
Efficiency and Speed
One of the prime benefits of using LVL formwork is the efficiency it brings to construction projects. The lightweight nature of LVL makes it easier to handle and transport, allowing crews to set up formwork more quickly than traditional methods. As a result, project timelines can be shortened, leading to significant cost savings.
Additionally, the pre-manufactured components of LVL formwork can be designed to specific project specifications, reducing the need for on-site adjustments and further expediting the construction process. This streamlined approach not only minimizes labor costs but also enhances overall productivity on the job site, allowing teams to focus on other critical tasks that contribute to project completion.
Versatility in Design
LVL formwork is incredibly versatile, suitable for various construction requirements. It can be customized to fit different shapes and sizes, making it ideal for both residential and commercial projects. From curved structures to flat surfaces, LVL can be tailored to meet specific architectural designs.
This adaptability not only provides creative freedom to architects and builders but also supports innovative construction techniques—further enhancing the potential applications of LVL formwork. Moreover, the ability to create complex geometries without compromising structural integrity opens up new avenues for modern architectural designs, allowing for more aesthetically pleasing and functional spaces. As the demand for unique and sustainable building solutions grows, LVL formwork stands out as a forward-thinking choice that aligns with contemporary construction trends.
LVL Formwork Maintenance and Care
Regular Inspection and Cleaning
To maximize the lifespan of LVL formwork, regular inspection and maintenance are critical. After each use, formwork should be checked for any visible signs of wear, damage, or moisture infiltration. A thorough cleaning process is essential to remove concrete residues and prevent build-up that could affect future applications.
Carrying out routine inspections helps in identifying potential issues before they escalate into significant problems, preserving the integrity of the LVL material over time. Additionally, it is advisable to document the condition of the formwork after each use, noting any repairs or maintenance performed. This record can be invaluable for tracking the performance of the formwork and planning for future maintenance needs. Click here to read more about integrity.
Proper Storage and Handling
The way LVL formwork is stored and handled can impact its longevity. Proper storage involves keeping the panels in a dry, covered area to shield them from environmental elements. Stacking them correctly also helps prevent warping or bending.
When handling LVL formwork, it’s crucial to use appropriate lifting techniques and equipment to avoid unnecessary stress on the materials. Following these guidelines ensures that the formwork remains in optimal condition for multiple uses. Furthermore, it’s beneficial to train all personnel involved in the handling and storage of LVL formwork on best practices. This training can include demonstrations on how to lift and transport the panels safely, as well as the importance of maintaining a clean and organized storage area to minimize the risk of damage.
Future of Construction: LVL Formwork
Technological Advancements and LVL Formwork
The future of construction looks promising with the continuous advancements in LVL technology. Innovations in adhesive development and veneer treatments are paving the way for even stronger and more durable LVL products. Manufacturers are exploring enhanced manufacturing techniques that not only improve the strength of LVL but also its eco-friendliness.
As the demand for more efficient construction materials grows, it’s likely that LVL formwork will evolve to meet complex engineering challenges, incorporating smart technologies to track performance metrics and improve usability during construction. For instance, the integration of IoT (Internet of Things) sensors could allow real-time monitoring of structural integrity, enabling builders to make informed decisions on-site. This could significantly reduce delays and enhance safety protocols, ensuring that projects remain on schedule and within budget.
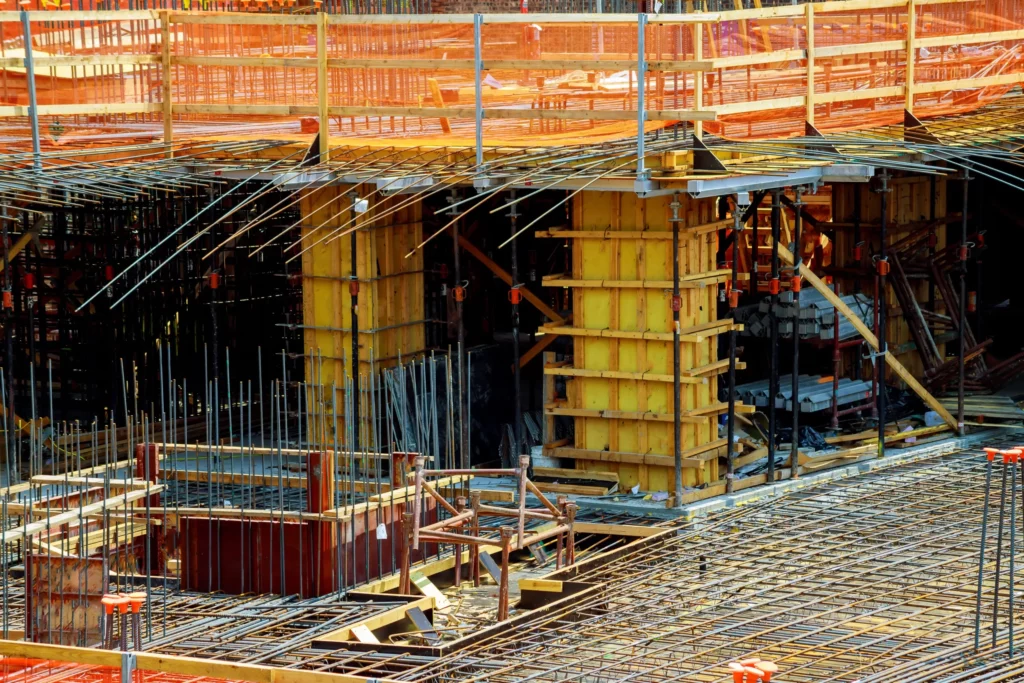
Sustainability and LVL Formwork
Environmental sustainability is becoming increasingly important in the construction industry. LVL formwork offers a sustainable solution, as it is primarily made from renewable resources. Furthermore, the efficient use of wood materials during the LVL production process minimizes waste and promotes responsible forestry practices.
With the additional consideration for recycling and reusing LVL formwork after its lifecycle, this material positions itself as a forward-thinking option for sustainable construction. This aspect aligns well with global initiatives aimed at reducing the environmental impact of building practices. Moreover, the carbon footprint of LVL is significantly lower compared to traditional concrete formwork, making it an attractive choice for environmentally conscious builders. As the industry moves towards more stringent regulations regarding sustainability, the adoption of LVL formwork could become a standard practice, further driving innovation in eco-friendly construction methods.
In addition to its environmental benefits, LVL formwork also supports the growing trend of modular construction. This approach not only speeds up the building process but also enhances precision and quality control, as components can be manufactured in a controlled environment before being assembled on-site. The synergy between LVL technology and modular construction could redefine how structures are built, leading to more resilient and adaptable buildings that meet the evolving needs of society.
In conclusion, LVL formwork presents significant advantages over traditional formwork systems, offering durability, efficiency, and versatility. As technology continues to advance and sustainability becomes a focal point, the future of LVL formwork in construction looks bright.
Read about lvl formwork at: LVL Timber Formwork Prices How to Get the Best Value